Facility maintenance work order software sets the stage for this enthralling narrative, offering a glimpse into a vital tool that enhances the management of maintenance tasks in various facilities. As technology continues to evolve, the role of software in facility management has become increasingly significant, providing solutions that optimize operational efficiency and cost-effectiveness.
By incorporating essential features such as tracking, reporting, and mobile access, this software empowers maintenance teams to communicate effectively and manage their workloads with ease. The benefits extend beyond mere task management, as organizations experience improved workflow and significant cost savings through streamlined processes.
Introduction to Facility Maintenance Work Order Software
Facility maintenance work order software serves as a crucial resource for organizations aiming to streamline their maintenance processes. This software enables businesses to efficiently manage maintenance tasks, ensuring that facilities remain in optimal condition. By digitizing the work order process, it reduces the complexity and time associated with traditional paper-based systems, enhancing overall productivity.The evolving role of technology in facility management is marked by a shift towards automation and data-driven decision-making.
In recent years, the integration of cloud computing, mobile applications, and IoT (Internet of Things) has transformed how maintenance tasks are tracked and executed. This technological advancement allows for real-time monitoring, predictive maintenance, and enhanced communication between facility managers and maintenance teams.
Key Features of Effective Facility Maintenance Work Order Software
Effective facility maintenance work order software is characterized by several features that contribute to its functionality and usability. Understanding these features is essential for organizations seeking to improve their maintenance operations.
- Work Order Management: A robust system allows for the creation, tracking, and management of work orders from initiation to completion. This includes assigning tasks to specific personnel and establishing deadlines.
- Preventive Maintenance Scheduling: The software can automate scheduling for routine inspections and maintenance tasks, helping to prevent equipment failure and prolong asset life.
- Inventory Management: Effective software keeps track of inventory levels for maintenance supplies, ensuring that necessary materials are available when needed, which minimizes downtime.
- Reporting and Analytics: This feature provides detailed insights into maintenance performance, allowing managers to analyze trends, costs, and resource allocation, leading to informed decision-making.
- Mobile Accessibility: Facility maintenance personnel can access the software via mobile devices, enabling them to receive updates, close out work orders, and report issues in real time, enhancing communication and efficiency.
“Investing in facility maintenance work order software empowers organizations to optimize their maintenance processes, reduce costs, and enhance the lifespan of their assets.”
Benefits of Using Work Order Software
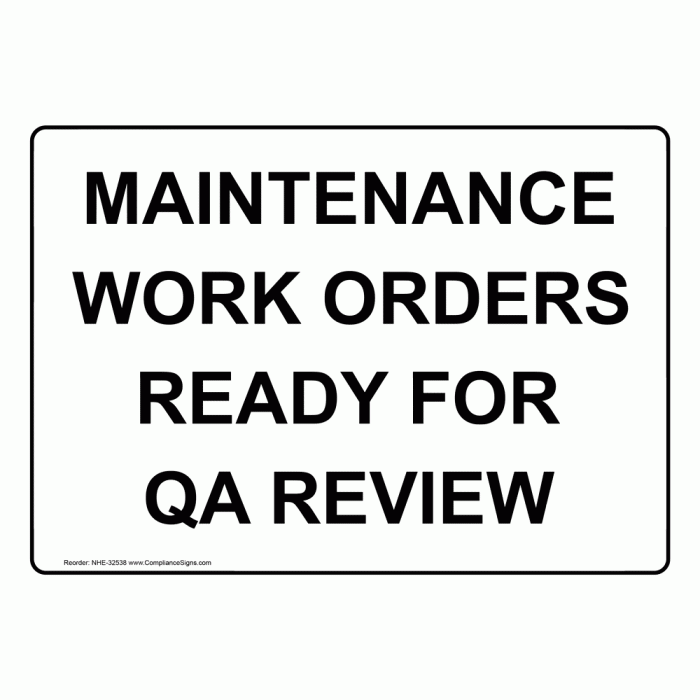
Source: compliancesigns.com
Work order software has increasingly become an integral tool in facility maintenance, streamlining operations and enhancing productivity. By automating various processes, this software allows maintenance teams to focus on high-priority tasks, ultimately leading to improved service delivery and satisfaction among stakeholders. The following sections illustrate how work order software can significantly benefit operational efficiency, cost management, and communication within maintenance operations.
Enhancement of Operational Efficiency
The implementation of work order software greatly boosts operational efficiency in facility maintenance. Tasks that once required manual tracking and paperwork can now be automated, resulting in quicker responses to maintenance requests. Maintenance teams can access real-time data, enabling them to prioritize tasks effectively and allocate resources accordingly. Additionally, scheduling maintenance activities becomes seamless, reducing downtime and increasing the overall productivity of facilities.
For example, a facility that previously relied on a paper-based system managed to cut down its response time to maintenance requests by 30% after implementing a work order software solution.
Cost Savings from Software Implementation
One of the most compelling advantages of adopting work order software is the potential for substantial cost savings. By streamlining processes and optimizing resource allocation, facilities can reduce operational costs significantly. For instance, a study showed that organizations using work order software experienced an average reduction of 20% in maintenance costs. This was achieved through smarter inventory management, reduction in overtime, and decreased equipment downtime.
Furthermore, predictive maintenance functionalities allow organizations to identify issues before they escalate, saving on costly repairs.
Improvements in Communication
Effective communication between maintenance teams and management is crucial for a successful facility operation. Work order software fosters improved communication channels by providing real-time updates on maintenance requests and project statuses. The following points highlight the key improvements in communication facilitated by work order software:
- Centralized communication platform for maintenance requests and updates.
- Instant notifications sent to relevant team members upon task assignment or status changes.
- Access to historical data for better decision-making and strategy formulation.
- Enhanced visibility of ongoing projects, allowing management to monitor progress and allocate resources more efficiently.
With these improvements, maintenance teams can operate more cohesively, leading to faster resolution times and a more organized workflow.
Key Features to Look for in Work Order Software
When selecting work order software, it’s essential to understand which features are crucial for efficient facility maintenance management. A well-designed system can streamline your operations, enhance communication, and ultimately save time and resources. This section delves into the key features that can significantly improve the process of managing work orders in any facility.One of the most important aspects of work order software is its ability to track and report on various tasks.
A comprehensive system should offer robust tracking capabilities that allow maintenance teams to monitor the status of work orders in real-time. This ensures accountability and helps identify any bottlenecks in the maintenance workflow. Additionally, reporting capabilities are vital for analyzing performance metrics, understanding resource allocation, and making informed decisions for future maintenance strategies.
Essential Features
Several key features are paramount when evaluating work order software. Below are some essential functionalities to consider:
- Work Order Tracking: Allows for real-time status updates on work orders, ensuring all team members are on the same page.
- Reporting and Analytics: Provides insight into maintenance performance through detailed reports, enabling data-driven decision-making.
- Asset Management: Facilitates the monitoring of equipment and assets, including maintenance history and scheduling.
- Mobile Access: Empowers maintenance staff to access information and update work orders on-the-go, increasing responsiveness.
- Integration Capabilities: Ensures seamless connection with other systems, such as inventory and financial software, for streamlined operations.
Comparison of Popular Software Options
To better understand the range of options available, here’s a comparison of several popular work order software solutions, highlighting their key features and pricing:
Software Name | Key Features | Pricing |
---|---|---|
FMX | Work order tracking, asset management, reporting | Starting at $35/month |
UpKeep | Mobile access, preventive maintenance, reporting | Starting at $35/user/month |
Hippo CMMS | Work order management, asset tracking, analytics | Starting at $39/month |
Maintenance Connection | Inventory management, mobile access, reporting | Contact for pricing |
Importance of Mobile Access
Mobile access is an integral feature of modern work order software. It allows maintenance staff to receive updates, access work orders, and input data directly from the field, leading to a more efficient workflow. This capability significantly reduces delays associated with communication, as technicians can immediately update the status of tasks and report issues. For example, a maintenance technician equipped with a mobile device can quickly check in to a job site, document any repairs made, and close out work orders without needing to return to the office.
This not only saves time but also enhances the accuracy of recorded information and improves overall productivity. As organizations increasingly adapt to remote and hybrid work environments, mobile access has become a crucial factor in the success of facility maintenance operations.
Implementation Strategies for Work Order Software
Implementing work order software can significantly enhance the efficiency of facility maintenance operations. However, a successful implementation requires careful planning and execution. This guide provides a step-by-step overview for organizations looking to adopt work order software, along with insights into common challenges and strategies to overcome them.
Step-by-Step Guide for Implementation
A structured approach to implementing work order software can streamline the process and minimize disruptions. Here’s a clear roadmap that organizations can follow:
- Define Objectives: Establish specific goals for what the organization aims to achieve with the new software. Clear objectives help guide the implementation process.
- Assess Current Processes: Analyze existing maintenance procedures and identify areas that can benefit from software integration. Understanding current workflows allows for a smoother transition.
- Select the Right Software: Choose software that aligns with the organization’s needs and objectives. Consider key features such as user-friendliness, scalability, and integration capabilities.
- Plan for Data Migration: Develop a strategy for transferring existing data into the new system. Ensure data accuracy and completeness to avoid future issues.
- Training and Development: Organize training sessions for staff to familiarize them with the new software. Proper training enhances user adoption and maximizes software benefits.
- Implement in Phases: Consider a phased rollout rather than a complete switch to the new system. This approach allows for adjustments based on feedback and can help mitigate risks.
- Monitor and Optimize: After implementation, continuously monitor the software performance and user feedback. Make necessary adjustments to improve efficiency and user experience.
Common Challenges and Overcoming Strategies
Organizations often face several challenges during the implementation of work order software. Understanding these challenges and having the right strategies can facilitate a smoother transition.
Resistance to change is a common barrier during software implementation.
Efforts to overcome this include:
- Involve Stakeholders: Engage key personnel early in the decision-making process to gain their support and insights.
- Communicate Benefits: Clearly articulate how the software will benefit the facility and make daily tasks easier for staff.
- Provide Ongoing Support: Offer continuous support and resources during the transition period to address concerns and questions.
Case Studies of Successful Software Implementation
Real-world examples can illustrate the effectiveness of work order software in various facilities. These case studies highlight the benefits derived from successful implementations.One notable case is a large university that implemented work order software to manage its maintenance needs across multiple campuses. By adopting a phased approach, the university was able to identify issues in real-time and improve response times for maintenance requests.
Over six months, they reported a 30% reduction in administrative workload and increased user satisfaction.Another example is a manufacturing facility that integrated work order software to streamline its maintenance management. With real-time tracking and analytics, the facility improved equipment uptime by 25% and reduced maintenance costs by 15% within the first year.These cases demonstrate that with proper planning, training, and support, organizations can reap significant benefits from work order software, enhancing overall operational efficiency and effectiveness.
Integration with Other Systems
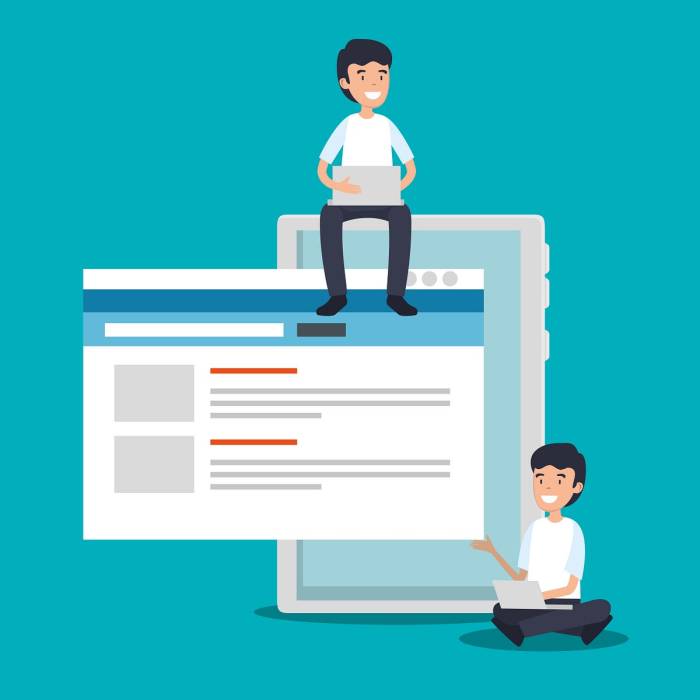
Source: medium.com
Integrating facility maintenance work order software with existing management systems can significantly enhance operational efficiency and data accuracy. By connecting work order software with systems such as Enterprise Resource Planning (ERP) or Computerized Maintenance Management Systems (CMMS), organizations streamline processes and ensure a seamless flow of information across departments. This integration facilitates better decision-making and resource management.The technical requirements for integrating work order software typically include compatible APIs (Application Programming Interfaces), data mapping protocols, and user authentication processes.
Establishing a successful integration involves identifying the key data points that need to be shared across systems, ensuring that both systems can communicate effectively, and testing the integration thoroughly to avoid any disruptions in operations. Additionally, organizations may need to invest in middleware or integration platforms that can bridge the gap between disparate systems.
Benefits of Integration
Integrating work order software with other management systems brings numerous advantages that can lead to enhanced efficiency, reduced costs, and improved service delivery. Some of the key benefits include:
- Improved Data Accuracy: Integration reduces the need for manual data entry, minimizing errors, and discrepancies in facility management records.
- Enhanced Reporting: Consolidated data allows for more comprehensive analytics and reporting, aiding in informed decision-making.
- Streamlined Processes: Automating workflows across systems leads to faster response times and improved coordination between departments.
- Cost Savings: By optimizing resource allocation and minimizing manual tasks, organizations can reduce operational costs significantly.
Technical Requirements for Successful Integration
Achieving a successful integration between work order software and existing systems requires careful planning and execution. Key technical requirements often include:
- API Availability: Both systems should provide accessible APIs that can facilitate data exchange.
- Data Mapping: A clear understanding of how data points from one system correspond to another is essential for effective integration.
- Security Protocols: Ensuring secure transmission of data between systems is crucial to protecting sensitive information.
- Testing Environment: Before full deployment, testing should be conducted to identify and address any potential issues.
Examples of Successful Integrations
Several real-world examples illustrate the positive impact of integrating work order software with other management systems:
- XYZ Corp: By integrating their work order software with their ERP system, XYZ Corp improved inventory management and reduced downtime by 30%. The automated updates on maintenance needs allowed for timely procurement of necessary supplies.
- ABC Facilities: ABC Facilities achieved a 25% reduction in administrative overhead by connecting their CMMS with their work order software, thereby automating scheduling and reporting processes.
Training and Adoption
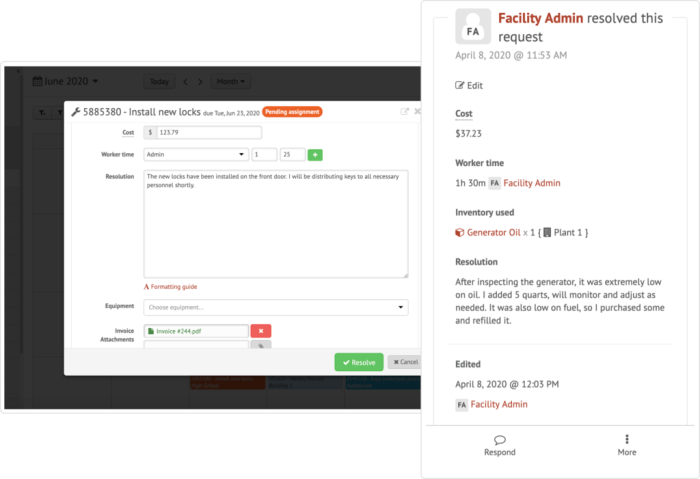
Source: gofmx.com
Implementing work order software is a significant step toward enhancing facility maintenance efficiency, but the journey doesn’t end with installation. Training staff on how to effectively use the software is crucial for maximizing its potential and ensuring a smooth transition. Proper training not only enables users to understand the functionalities of the software but also fosters confidence in their ability to adapt to new technologies.Ongoing support and resources post-implementation play a vital role in reinforcing the skills learned during training.
This continuous learning approach is essential, as staff can encounter challenges or have questions as they begin to incorporate the software into their daily routines.
Training Requirements for Staff
To ensure that staff can operate the work order software effectively, a comprehensive training program should be established. This program should cover a variety of aspects, from basic navigation to more complex functionalities. Consider the following elements when designing training sessions:
- Initial Training Sessions: Conduct hands-on training sessions that allow staff to interact with the software in real-time. Use scenarios that mimic everyday tasks to make the training practical and relatable.
- User Manuals and Documentation: Provide detailed user manuals and online resources that staff can refer to after the initial training. This material should be easily accessible and written in straightforward language.
- Role-Specific Training: Tailor training sessions to different roles within the maintenance team. For instance, technicians may require training focused on task execution, while managers may benefit from learning about analytics and reporting features.
- Training Schedules: Establish a flexible training schedule that accommodates all staff members. Consider different shifts and workloads to ensure everyone has the opportunity to participate.
Encouraging Adoption Among Maintenance Personnel
Fostering a culture of innovation and openness to change is essential for encouraging the adoption of work order software among maintenance personnel. The following strategies can be beneficial:
- Highlighting Benefits: Regularly communicate the advantages of using the software, such as improved task tracking, reduced downtime, and enhanced communication. Create a sense of excitement around the positive impact on their work.
- Involve Staff in the Process: Engage maintenance personnel in the decision-making process during software selection and implementation. Their feedback can ensure that the software meets their needs and increases their buy-in.
- Recognition and Incentives: Implement recognition programs or incentives for staff who actively engage with the software or help others learn. This can motivate personnel to embrace the new system.
Ongoing Support and Resources for Users
After the implementation of work order software, continuous support is crucial for maintaining user engagement and proficiency. Providing ongoing resources can significantly enhance user experience:
- Help Desks and Support Teams: Establish a dedicated support team to assist users with any challenges they face. A help desk that is easily reachable can alleviate frustrations and encourage continuous usage.
- Regular Check-ins and Refresher Courses: Schedule periodic check-ins to address any difficulties staff may encounter and offer refresher courses to help reinforce skills as needed.
- User Feedback Mechanisms: Create channels for users to provide feedback on the software. This information can be invaluable for making necessary adjustments and improving user satisfaction.
“Investing in training and support not only increases the likelihood of successful software adoption but also enhances overall productivity and morale within the team.”
Future Trends in Facility Maintenance Software
As technology continues to advance, facility maintenance software is evolving to meet the changing needs of organizations. Emerging technologies such as Artificial Intelligence (AI) and the Internet of Things (IoT) are beginning to play a crucial role in shaping the future landscape of work order software. Understanding these trends is essential for businesses looking to enhance their facility management processes.One of the significant influences on future facility maintenance software is the integration of AI and machine learning.
These technologies have the potential to automate routine tasks, predict maintenance needs, and analyze data more effectively. As organizations seek efficiency and cost savings, the demand for software that can learn from historical data and optimize maintenance schedules will increase. The following key trends are expected to shape the future of facility maintenance software:
Emerging Technologies Influencing Facility Maintenance
The incorporation of advanced technologies into facility maintenance software will bring several advantages. Here are some notable trends:
- Artificial Intelligence: AI-enabled systems can provide predictive analytics, allowing facilities to foresee potential equipment failures and schedule maintenance before issues arise. For instance, predictive maintenance in industrial setups has been shown to reduce downtime by up to 30%.
- Internet of Things (IoT): IoT devices monitor equipment and environmental conditions in real-time, providing valuable insights that drive informed decision-making. Smart sensors can detect changes and trigger work orders automatically, streamlining the maintenance process.
- Mobile Technology: The shift towards mobile applications will enable technicians to access work orders, report issues, and update statuses on the go. This mobility enhances communication and speeds up response times.
- Cloud Computing: Cloud-based solutions will continue to grow, offering flexibility and scalability. Facilities can easily access data and collaborate across teams, enhancing overall operational efficiency.
User Expectations and Demands for Future Software Developments
As users become more tech-savvy, their expectations for facility maintenance software are evolving. Some anticipated user demands include:
- Intuitive Interfaces: Users expect modern software to have user-friendly interfaces that simplify navigation and minimize training time.
- Enhanced Analytics: Organizations are looking for advanced reporting capabilities that provide actionable insights, allowing for better decision-making based on real-time data.
- Customization: Users desire the ability to tailor software features and functionality to meet the specific needs of their facilities.
- Integration Capabilities: Future software must seamlessly integrate with existing systems, such as ERP and asset management tools, to create a cohesive operational environment.
Potential Challenges with Advancements in Technology
While the future of facility maintenance software appears promising, several challenges may arise with technological advancements:
- Data Security: As systems become more connected, concerns regarding data privacy and security will intensify. Organizations will need to invest in robust security measures to protect sensitive information.
- Implementation Costs: The transition to advanced software solutions may involve significant upfront costs, which could deter some organizations from making the leap.
- Resistance to Change: Employees accustomed to traditional methods may resist adopting new technologies, necessitating comprehensive training and change management strategies.
- Complexity of Integrations: Integrating new technologies with legacy systems can be complex and may require specialized expertise.
Wrap-Up
In summary, the discussion around facility maintenance work order software highlights its crucial role in modern facility management. As organizations embrace these technological advancements, they can expect enhanced efficiency, better communication, and a more seamless integration of maintenance tasks into their overall operations. Looking ahead, the future of this software promises to be shaped by emerging technologies, presenting exciting opportunities and challenges for facilities worldwide.
FAQ Explained: Facility Maintenance Work Order Software
What is facility maintenance work order software?
It is a digital tool designed to help organizations manage maintenance requests and workflows efficiently.
How does work order software improve communication?
It facilitates real-time updates and information sharing between maintenance teams and management, reducing miscommunication.
Is mobile access important for maintenance staff?
Yes, mobile access allows staff to manage tasks on the go, enhancing productivity and response times.
What are common challenges during implementation?
Challenges can include resistance to change, lack of training, and integration issues with existing systems.
How can staff be encouraged to adopt new software?
Providing thorough training, ongoing support, and demonstrating the software’s benefits can help increase adoption rates.